Exploring Quality Management Systems: A Comprehensive Guide
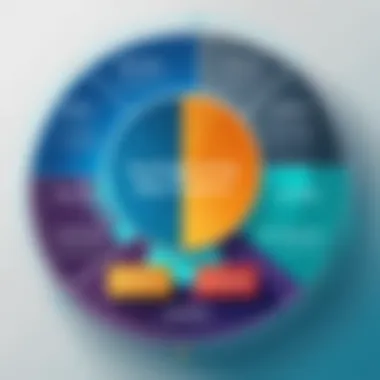
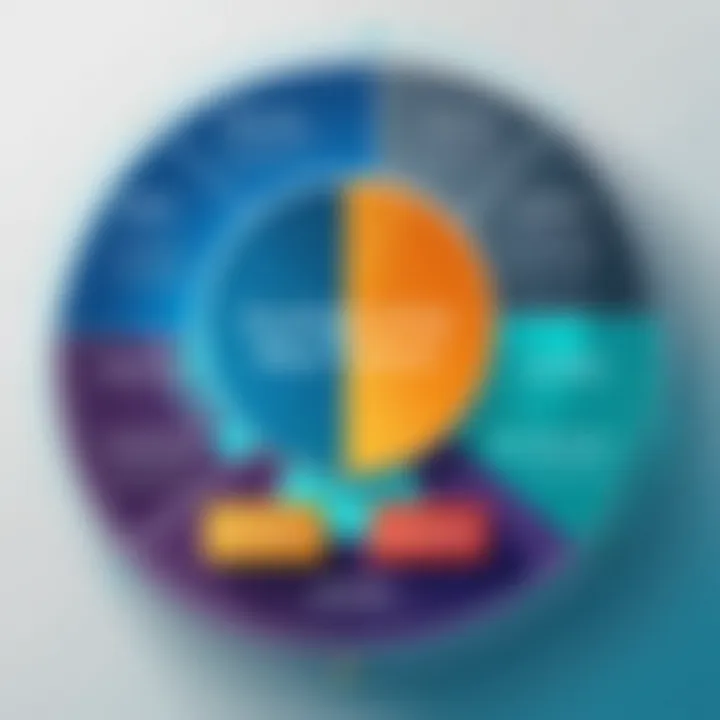
Intro
Quality Management Systems (QMS) serve a fundamental role in today's business landscape. They guide organizations in enhancing efficiency, increasing customer satisfaction, and improving overall product quality. In a rapidly changing environment, understanding and implementing a robust QMS has become vital for maintaining a competitive advantage. This article dives into various components of Quality Management Systems, including their significance, models, methodologies, challenges, and future trends.
Organizations consistently strive for operational excellence. As such, QMS frameworks offer a structured approach that can adapt to various industries. By applying principles of quality management, businesses can streamline processes, reduce waste, and respond more effectively to customer needs.
In the following sections, we will discuss the software overview, examining its key features and system requirements that any organization should consider prior to implementation. An in-depth analysis will provide insights on performance, usability, and best use cases for QMS solutions. This careful look at quality management systems will empower professionals and students alike to make informed decisions for implementation and optimization.
Software Overview
Quality Management Software (QMS) integrates various processes and tools to help organizations achieve their quality objectives. Understanding key features and system requirements is crucial for selecting an effective solution.
Key Features
When assessing QMS software, consider the following features:
- Document Control: Efficient management and tracking of documents to ensure compliance and quality.
- Audit Management: Tools to facilitate both internal and external audits, ensuring adherence to standards.
- Non-Conformance Tracking: Recording and monitoring non-conformance issues and corrective actions.
- Training Management: Tracking employee training and competencies related to quality procedures.
- Reporting and Analytics: Providing insights into quality metrics to support data-driven decisions.
System Requirements
Before selecting a QMS software, it is essential to evaluate the system requirements. Commonly, these may include:
- Operating System: Most QMS solutions are compatible with Windows, macOS, and Linux.
- Database Support: Options such as SQL Server or Oracle Database may be required for better data management.
- Browser Compatibility: Ensure compatibility with major browsers like Chrome, Firefox, or Safari for web-based solutions.
- Network Infrastructure: A reliable internet connection is necessary for cloud-based QMS tools.
In-Depth Analysis
Performance and Usability
Performance metrics help gauge the efficiency of a QMS solution. Key indicators include:
- Speed: The loading times for various functionalities in the software should be minimal.
- Scalability: The ability to grow with the organization, easily accommodating new processes and users.
- User Experience: Intuitive interface design and navigation enhance usability for all users.
Understanding how the software performs can significantly impact its success within an organization.
Best Use Cases
Quality Management Systems can be beneficial across various sectors. Some notable use cases include:
- Manufacturing: Ensuring product quality and regulatory compliance through systematic processes.
- Healthcare: Maintaining high standards of patient care through stringent quality protocols.
- Food Industry: Managing food safety and hygiene standards effectively.
"A well-implemented QMS not only facilitates compliance but also fosters a culture of continuous improvement and excellence."
Organizations investing in Quality Management Systems position themselves to adapt and thrive in an ever-evolving marketplace.
Foreword to Quality Management Systems
Quality Management Systems (QMS) are integral to the operational success of any organization. In a competitive landscape, maintaining high-quality standards is essential for achieving customer satisfaction and business sustainability. QMS not only provides a framework for consistent quality but also fosters a culture of continuous improvement, making processes more efficient and effective. This section unpacks the significance of Quality Management Systems in today's business environment, emphasizing their role in enhancing organizational performance and cultivating customer trust.
Definition and Purpose
A Quality Management System is a structured system that outlines how an organization can achieve its quality policy and quality objectives. At its core, the purpose of a QMS is to systematically manage the quality of products and services while ensuring compliance with regulatory requirements. This involves a series of processes, procedures, and responsibilities that are designed to enhance customer satisfaction through consistent quality assurance.
The primary benefits of implementing a QMS include:
- Improved Efficiency: Streamlines operations and minimizes waste.
- Enhanced Customer Satisfaction: Ensures products meet customer expectations.
- Regulatory Compliance: Helps adhere to industry regulations.
- Data-Driven Decision Making: Facilitates informed strategies based on measurable results.
In a rapidly evolving market, the emphasis on quality cannot be overstated. Organizations that adopt a solid QMS can not only meet customer demands but also strategically position themselves for sustainable growth.
Historical Context
Understanding the historical evolution of Quality Management Systems is crucial for grasping their current frameworks and methodologies. The roots of quality management can be traced back to the early 20th century, with pioneers such as W. Edwards Deming and Joseph Juran laying the groundwork for modern QMS practices. The focus during these early years was largely reactive, aimed at detecting defects after they occurred.
However, as the marketplace became increasingly competitive, a shift occurred towards proactive quality management. This transition emphasized the importance of preventing defects before they appeared, thereby enhancing the overall quality of products and services. Key developments included:
- The introduction of Total Quality Management (TQM) in the 1980s, which promoted a holistic approach to quality across all organizational levels.
- The establishment of the ISO 9000 standards in 1987, which provided a standardized framework for QMS and quality assurance practices worldwide.
These milestones reflect a significant change in how organizations view quality; it is now seen as a fundamental aspect of strategic management rather than just a compliance requirement. As we move forward, it will be crucial to understand how these historical influences shape present-day QMS practices and their applications across different industries.
Core Principles of Quality Management
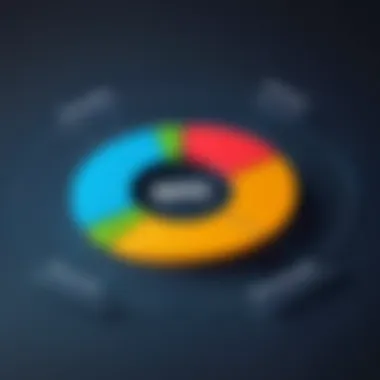
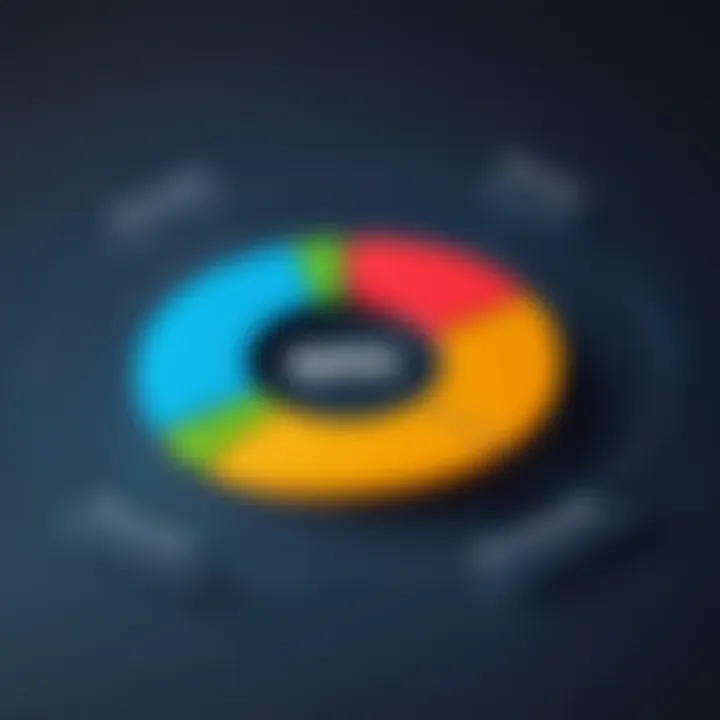
Quality Management Systems (QMS) serve as the backbone for organizations striving for excellence. To navigate this landscape effectively, understanding the core principles of quality management is essential. These principles not only set the foundation of a QMS but also guide its implementation and continuous evolution. They foster an environment where quality is a shared responsibility and an integral part of organizational culture. In this exploration, we will discuss key elements such as customer focus, leadership engagement, process orientation, continuous improvement, fact-based decision making, and mutual supplier relationships.
Customer Focus
Central to any successful QMS is a relentless focus on the customer. Organizations need to understand customer requirements and strive to exceed expectations. This customer-centric approach is not merely a response to feedback; it involves anticipating needs and ensuring that products or services consistently deliver value. A thorough understanding of customer demographics, preferences, and pain points enables organizations to tailor their offerings accordingly. Therefore, engaging with customers regularly through surveys, focus groups, and direct interactions is critical. It helps in refining products and enhancing service quality.
Leadership and Engagement
Leadership plays a pivotal role in promoting a culture of quality. Effective leaders cultivate an environment where quality management is prioritized. They inspire teams to align their goals with the organization’s vision. A leader's involvement in quality initiatives, communication, and engagement fosters a collective commitment to excellence. Moreover, when leaders actively participate in quality management activities, it motivates employees to embrace their responsibilities. By emphasizing the importance of quality, leaders help to establish accountability and transparency throughout the organization.
Process Approach
Taking a process approach is essential to understanding how work gets done within an organization. A well-structured process can identify areas where improvements are needed. This principle emphasizes planning, executing, and monitoring processes systematically. Organizations should map out key processes to discern workflows and inter-dependencies. By doing so, they can better manage outputs, resources, and risks. A consistent process approach leads to greater efficiency and effective resource allocation. It allows businesses to achieve predictable outcomes that align with strategic goals.
Continuous Improvement
To remain competitive, organizations must commit to continuous improvement. This principle involves the ongoing enhancement of processes, products, and services. It requires a proactive attitude toward assessing and optimizing performance. Adopting frameworks such as Plan-Do-Check-Act (PDCA) can facilitate this journey. Regular review cycles help to identify gaps and areas for improvement. Furthermore, creating a feedback loop encourages collaboration and innovation within teams. Continuous improvement is a dynamic process that cultivates resilience against market fluctuations and customer demands.
Fact-Based Decision Making
Data-driven decision making is at the heart of effective quality management. Organizations must rely on quantitative metrics to guide their choices rather than assumptions. Analyzing relevant data allows businesses to spot trends, understand customer behaviors, and measure performance. This principle stresses the importance of collecting, analyzing, and interpreting data systematically. Using techniques like dashboards and performance metrics helps organizations make informed decisions that drive quality improvements and operational efficiency.
Mutually Beneficial Supplier Relationships
A well-functioning quality management system recognizes that suppliers are an extension of the organization. Building mutually beneficial relationships with suppliers leads to improved collaboration and trust. Close engagement with suppliers allows for the sharing of information, resources, and expertise. This partnership can enhance product quality, reduce costs, and streamline processes. Organizations should establish clear communication channels and performance expectations with suppliers to ensure alignment with quality goals. Investing in these relationships pays off through improved quality and innovation in the long run.
"Quality is not an act, it is a habit." - Aristotle
Quality Management Frameworks
Quality Management Frameworks serve as structured approaches to achieving optimal quality within organizations. These frameworks are essential because they provide a clear guideline for implementing and maintaining a Quality Management System (QMS). By adhering to established standards, organizations can effectively improve processes, enhance products or services, and ultimately increase customer satisfaction. Different frameworks offer various principles and practices that cater to different organizational needs, making them versatile tools in the pursuit of quality excellence.
ISO Overview
ISO 9001 is one of the most widely recognized and implemented quality management standards globally. The standard focuses on a set of requirements that organizations must follow to ensure consistent quality in their products and services. The main principle of ISO 9001 is to increase customer satisfaction through effective system management. Organizations aiming for this certification must demonstrate their ability to consistently provide products that meet both customer and regulatory requirements.
Benefits of ISO include:
- Improved operational efficiency
- Enhanced customer trust and satisfaction
- Streamlined processes and reduced waste
- Increased employee engagement and morale
Lean Management
Lean Management focuses on maximizing value by eliminating waste. This framework emphasizes continual improvement and seeks to enhance customer value with fewer resources. The core principle is to understand what creates value for the customer and to optimize operational processes accordingly. For software developers and IT professionals, applying lean principles can lead to faster delivery times and higher quality software products.
Key elements of Lean Management involve:
- Value stream mapping: Identifying all the steps in a process and optimizing them.
- Continuous flow: Ensuring that products flow smoothly through each stage.
- Pull systems: Producing only what is needed, when it is needed.
Six Sigma Principles
Six Sigma is a data-driven approach aimed at reducing defects and improving quality in any organizational process. By employing statistical methods, Six Sigma focuses on eliminating variability, thus ensuring a consistent outcome. Six Sigma utilizes the DMAIC framework which stands for Define, Measure, Analyze, Improve, and Control. Each phase is critical in driving improvements and achieving quality objectives.
Six Sigma offers numerous benefits, such as:
- Reduction in process variations leading to greater consistency.
- Improved customer satisfaction through superior quality.
- Increased profitability by minimizing waste and defects.
Total Quality Management (TQM)
Total Quality Management is a holistic approach to long-term success through customer satisfaction. TQM incorporates all members of an organization and promotes a culture that strives for continuous improvement. It emphasizes the importance of total involvement from all employees in achieving high-quality standards.
Key aspects of TQM include:
- Employee empowerment: Ensuring all employees have the training and resources to contribute to quality.
- Customer focus: Understanding customer needs and striving to exceed expectations.
- Process approach: Managing and improving processes consistently across the organization.
In summary, choosing the right quality management framework can foster an environment conducive to continuous improvement. Organizations can achieve better overall performance by aligning strategies with these frameworks.
The Role of Technology in QMS
In contemporary business environments, technology plays a crucial role in enhancing Quality Management Systems (QMS). A well-implemented technology strategy can streamline processes, reduce errors, and improve overall efficiency. Incorporating advancements in technology allows organizations to better meet customer demands and maintain competitive advantages. The integration of technology in QMS also means that organizations can respond swiftly to changes in market conditions and ensure that quality standards evolve accordingly.
Automation Tools
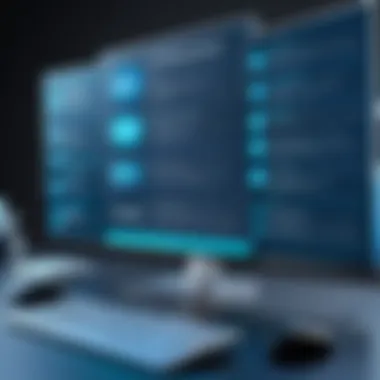
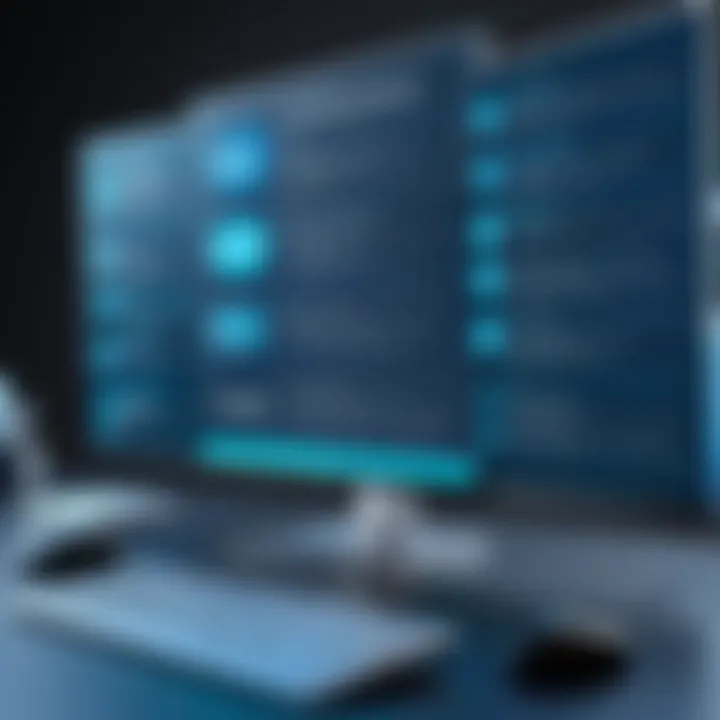
Automation tools are essential in modern QMS. They help in standardizing processes, which leads to increased consistency and reliability. For example, tools that automate inspection processes can catch defects sooner, reducing waste and rework.
The benefits of automation tools include:
- Increased efficiency: Tasks that were previously manual can be executed faster, allowing employees to focus on value-added activities.
- Reduced human error: Automated systems minimize the chances of mistakes that can occur in manual processes.
- Real-time monitoring: Organizations can instantly track performance metrics and take corrective actions if necessary.
Examples of popular automation tools include software like QA Complete and TestRail. These platforms facilitate automated testing and quality checks, ensuring that standards are upheld throughout production.
Data Analysis and Reporting
Data analysis and reporting are integral for any effective QMS. They provide insights into performance metrics, enabling organizations to make informed decisions. Data analytics allows for the identification of trends, highlighting areas for improvement.
Utilizing data in QMS provides the following advantages:
- Informed decision-making: Organizations can analyze data to understand the root causes of quality issues and implement corrective measures.
- Trend identification: Analytics help reveal patterns over time that could signify underlying problems.
- Enhanced reporting capabilities: Modern tools allow for comprehensive reporting, enabling stakeholders to grasp the current quality landscape easily.
For instance, platforms such as Tableau and Microsoft Power BI present data in a visual format, which simplifies the analysis process.
Cloud-Based Solutions
Cloud-based solutions are changing how organizations implement and manage QMS. These platforms offer scalable solutions that adjust to an organization’s needs while ensuring data security and accessibility.
Some benefits of adopting cloud-based solutions include:
- Accessibility: Users can access quality management tools from anywhere, promoting collaboration across teams and locations.
- Cost efficiency: Companies can reduce IT infrastructure costs by using cloud services, often on a subscription basis.
- Regular updates: Cloud solutions are maintained by the service provider, ensuring that users always have access to the latest features and security enhancements.
Popular cloud-based QMS software includes QMS ISO and Qualio, which provide integrated platforms for quality management.
Adopting these technologies effectively can dramatically transform an organization's approach to quality management.
In summary, the role of technology in QMS cannot be overstated. Automation tools, data analysis, and cloud-based solutions work together to create an agile, responsive, and efficient quality management framework, equipping organizations to thrive in today's fast-paced business landscape.
Implementation of a Quality Management System
Implementing a Quality Management System (QMS) is crucial for any organization aiming to enhance operational efficiency and improve customer satisfaction. A well-implemented QMS ensures that processes are standardised, predictable, and continuously improved. By defining clear procedures and expectations, organizations can minimize variances in products and services. This not only boosts overall quality but also fosters a culture of accountability and excellence within teams.
The benefits of proper implementation are vast. It helps in establishing a systematic approach to quality, enhances compliance with regulations, and significantly increases customer trust. Furthermore, organizations can identify areas for improvement through data-driven insights and continuous monitoring. However, several considerations must be taken into account during the implementation phase to avoid common pitfalls that can lead to ineffective systems.
Steps for Effective Implementation
- Define Objectives: Clearly outline what the organization aims to achieve with the QMS. This could include reducing defects, improving customer satisfaction, or streamlining processes.
- Engage Stakeholders: Involve employees at all levels. Their insights can provide valuable perspectives on existing processes and potential improvements.
- Choose the Right Framework: Depending on industry and goals, select a quality framework such as ISO 9001 or Total Quality Management. Each framework has unique features and compliance requirements.
- Develop Processes: Draft documents that outline standard operating procedures (SOPs). Make sure these documents are accessible and understandable to all relevant personnel.
- Implement Training: Conduct training sessions for employees to familiarize them with the QMS procedures and the importance of their roles.
- Monitor Progress: Put in place mechanisms for monitoring progress. This can include regular audits and reviews to ensure that the QMS is functioning as intended.
- Review and Revise: Utilize feedback for continuous improvement. The QMS should be a living system, adapting to changes in the business environment or regulatory requirements.
Role of Training and Development
Training and development are pivotal in the successful implementation of a Quality Management System. To ensure that employees understand the framework and procedures, structured training programs must be developed.
Training should cover:
- QMS Principles: Enlighten employees about the core principles of the QMS, highlighting its purpose and benefits.
- Procedural Knowledge: Provide specific instructions on the procedures relevant to their job functions.
- Feedback Mechanism: Encourage an open-door policy for employees to report challenges and suggest improvements to the QMS processes.
Incorporating regular training sessions not only reinforces the importance of the QMS but also enhances employee morale. Employees who understand how their roles contribute to organizational goals are likely to be more engaged and committed.
"An effective quality management system relies heavily on knowledgeable and capable personnel. Training is not merely a checkbox; it is the foundation of success in any QMS implementation."
Challenges in QMS Adoption
Integrating a Quality Management System (QMS) into an organization's operations is an essential step towards achieving quality enhancement. However, this process does not come without significant challenges. Understanding these difficulties is crucial for fostering a smoother transition and ensuring long-term effectiveness. Here, we explore two primary challenges: resistance to change and resource constraints.
Resistance to Change
Resistance to change is a pervasive challenge in adopting a QMS. Many organizations face pushback from employees who are accustomed to their current processes. This resistance often stems from fear of the unknown and concerns about job security. Change can be intimidating, especially in a workplace that has operated in a certain manner for an extended period.
Strategies to Mitigate Resistance
Organizations can implement several strategies to address resistance:
- Communication: Clear communication about the benefits of QMS is vital. Employees should understand how QMS will improve their work environment and lead to a more efficient organization.
- Involvement: Involving employees in the QMS design and implementation can reduce anxiety. When employees feel they have a stake in the process, they are more likely to accept changes.
- Training: Offering comprehensive training can ease anxiety. Familiarizing staff with new processes and tools can reduce resistance and boost confidence.
Supervisors should actively engage with their teams throughout the implementation, creating an atmosphere where feedback is encouraged. This approach fosters collective ownership of the QMS.
"Change is constant; the growth is optional. Embrace it to move forward."
Resource Constraints
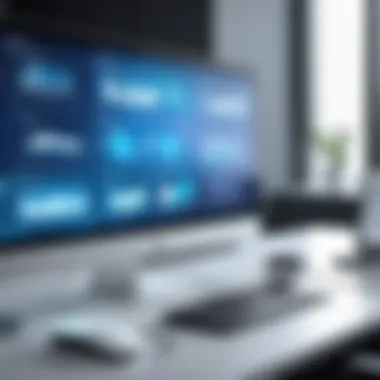
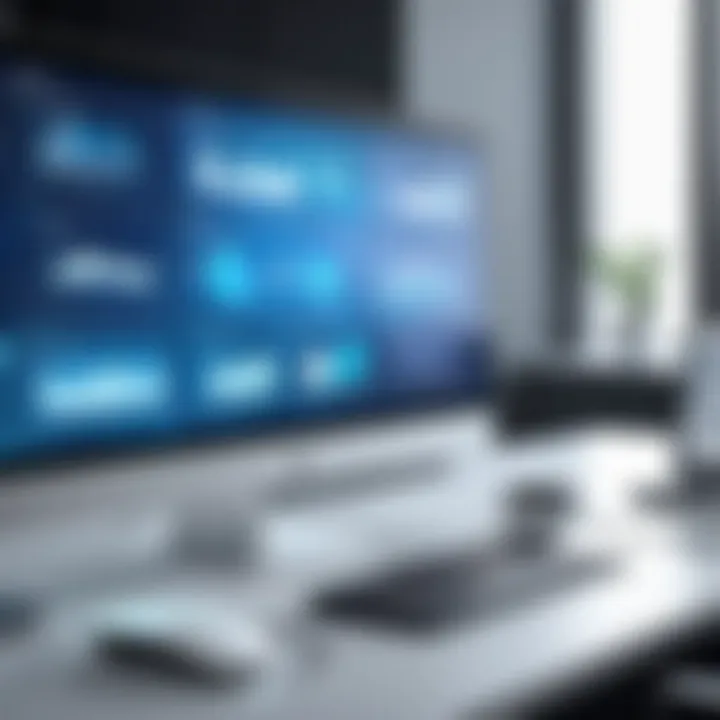
Resource constraints also pose a significant challenge to the adoption of a QMS. Organizations may find themselves limited by financial, human, or technological resources. Limited budgets can restrict the ability to purchase the necessary tools, systems, or training required for effective QMS implementation.
Furthermore, staff shortages can hinder the commitment to training and ongoing support needed in the early stages of QMS adoption. Instability in staffing or lack of key personnel can disrupt the QMS initiative, leading to inadequate understanding and implementation of the system.
To combat these constraints, organizations may look into:
- Prioritizing investments: It can be beneficial to prioritize the most impactful aspects of QMS that align with organizational goals, ensuring resources are allocated effectively.
- Leveraging existing tools: Utilizing current technologies or processes can reduce initial costs. Assessing existing capabilities can uncover valuable resources that can facilitate QMS implementation.
- Phased implementation: Gradually rolling out the QMS allows organizations to manage resources more effectively. This strategy can provide manageable changes over time, minimizing operational disruptions.
In summary, recognizing and addressing these challenges is essential for organizations seeking to establish a QMS. Resistance to change and resource constraints can derail efforts if not properly managed, yet with thoughtful planning and engagement, organizations can successfully navigate these hurdles.
Measuring the Effectiveness of QMS
An effective Quality Management System (QMS) is pivotal to the success of any organization. The efficacy of a QMS determines not just compliance with quality standards but also enhances overall operational performance. Measuring this effectiveness is crucial for identifying areas of improvement, ensuring that organizational goals meet customer expectations, and fostering a culture of continuous improvement.
To assess a QMS effectively, organizations must implement strategies that reflect their specific processes and objectives. This can include examining every phase of the system, from planning to execution and monitoring. By delving into quantifiable metrics, organizations can derive actionable insights that inform operational enhancements and strategic decisions.
Key Performance Indicators (KPIs)
Key Performance Indicators (KPIs) serve as a quantitative framework that allows organizations to measure the effectiveness of their QMS. These indicators help in tracking performance in various domains such as process efficiency, compliance with standards, and customer satisfaction.
Some common KPIs relevant to QMS include:
- Defect rates: Measurement of defect occurrences in products and services.
- Customer complaints: The volume and nature of complaints received can indicate areas for improvement.
- On-time delivery: Evaluation of whether products or services are delivered on promised timelines.
- Cost of quality: Analysis of the costs associated with ensuring quality versus the costs incurred due to defects.
Utilizing KPIs allows organizations to maintain a focus on their strategic objectives while enabling them to respond dynamically to operational improvements.
Customer Feedback and Satisfaction Surveys
Customer feedback is an invaluable source of information that reflects the quality of products and services provided by an organization. Regularly conducting satisfaction surveys enables organizations to gauge consumer sentiment and make informed adjustments to their QMS.
Surveys can include questions that assess:
- Overall satisfaction with products or services.
- The likelihood of recommending the organization to others.
- Specific areas for improvement or additional products/services desired by customers.
Customer feedback not only highlights strengths and weaknesses in a QMS but also fosters a relationship between the organization and its clientele. By integrated insights from feedback, organizations can enhance their processes and operational strategies to better align with customer expectations.
Future Trends in Quality Management Systems
Quality Management Systems (QMS) are continuously evolving to adapt to new challenges and technological advancements. As organizations strive for operational efficiency and enhanced customer satisfaction, it is essential to explore the potential future trends shaping QMS. Understanding these trends can help organizations stay proactive and competitive, ensuring they respond adeptly to both market demands and internal needs.
Integration with Artificial Intelligence
Artificial Intelligence (AI) is poised to transform various sectors, including quality management. The integration of AI into QMS offers numerous benefits:
- Data Analysis: AI can analyze vast datasets more efficiently than traditional methods. This capability allows organizations to identify patterns, assess risks, and pinpoint areas for improvement.
- Predictive Analytics: Using AI, organizations can leverage predictive analytics to foresee potential quality issues before they arise. This foresight enables proactive measures, which is preferable to reactive solutions.
- Automation of Routine Tasks: AI can automate repetitive processes such as data entry and reporting, freeing up personnel to focus on more strategic tasks. This shift enhances efficiency and productivity.
However, integrating AI into QMS also comes with considerations. Organizations must ensure they have the appropriate infrastructure and trained personnel to manage and utilize AI tools effectively. There is also a need for a significant cultural shift within the organization to fully embrace the benefits AI offers.
Emphasis on Sustainability
Sustainability has become not just a regulatory requirement but a corporate responsibility. Increasingly, organizations integrate sustainable practices into their QMS for several key reasons:
- Consumer Demand: Customers are now more informed and often prefer products and services from environmentally conscious companies. A commitment to sustainability can improve brand loyalty and customer satisfaction.
- Regulatory Compliance: Governments are enforcing stricter regulations regarding environmental responsibility. Organizations that align their QMS with sustainable practices can better navigate these regulations and avoid potential penalties.
- Resource Efficiency: Implementing sustainable practices often correlates with more efficient resource use, which can reduce costs in the long run.
To implement sustainability into QMS, organizations should consider developing sustainability metrics and integrating them into existing quality control processes. This integration requires organizations to continuously monitor their ecological impact and streamline operations to minimize waste.
"The integration of sustainability within QMS is not just about compliance; it is a strategic advantage that aligns with modern consumer expectations."
By recognizing these future trends, organizations can enhance their QMS, ensuring they remain effective in meeting quality standards while also advancing toward a more sustainable and technologically forward approach.
Finale
The conclusion of this article serves to distil the essential insights regarding Quality Management Systems (QMS). Understanding the topic is crucial for various stakeholders in today’s competitive landscape. Organizations must recognize that implementing a robust QMS can lead to significant improvements in efficiency and customer satisfaction. Quality management is not just a compliance issue; it's a strategic initiative that can drive business success.
Summarizing Key Points
In summary, we have explored several important aspects throughout this article:
- Definition and Purpose: A QMS provides a structured approach to managing organizational processes to consistently deliver quality products or services.
- Core Principles: Emphasizing customer focus, continuous improvement, and engaging leadership is key to any successful QMS.
- Frameworks: ISO 9001, Lean Management, Six Sigma, and Total Quality Management offer diverse methodologies that can be tailored to various sectors.
- Technology’s Role: Automation, data analysis, and cloud solutions represent the modern tools that enhance QMS efficiency.
- Implementation Challenges: Resistance to change and resource constraints can hinder effective QMS adoption.
- Future Trends: The integration of artificial intelligence and sustainability are shaping the future of quality management.
Collectively, these points illustrate that an effective QMS is integral to operational success and customer loyalty.
Call to Action for Organizations
Organizations are encouraged to prioritize the development and continuous refinement of their Quality Management Systems. This should not be viewed merely as a regulatory requirement but as an opportunity to foster improvement across all areas of the business.
- Conduct a QMS Assessment: Evaluate current processes to identify areas for improvement and align them with best practices.
- Invest in Training: Equip employees with the necessary skills to engage with QMS methodologies effectively.
- Leverage Technology: Utilize modern tools and software to streamline processes and provide insightful data analysis.
- Engage Stakeholders: Foster an organizational culture that promotes collaboration between management and employees for a more effective QMS.
- Monitor and Adapt: Regularly measure performance against established KPIs and be prepared to adapt strategies in response to feedback and changing conditions.