Exploring the Phantom Auto Forklift: Innovation in Material Handling
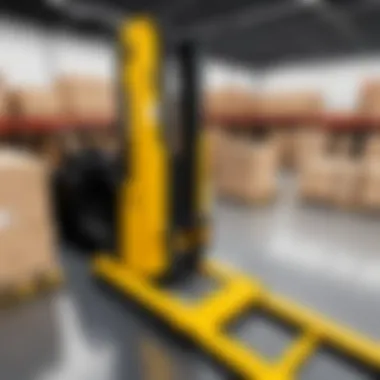
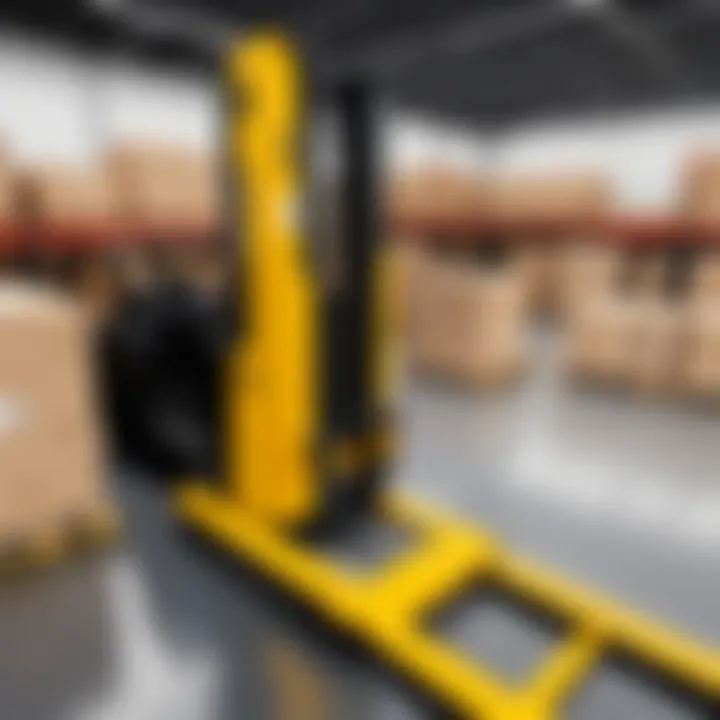
Intro
In the realm of material handling, efficiency and safety are the cornerstones of progress. Amidst the rapid evolution of industry technologies, the introduction of the Phantom Auto Forklift marks a significant leap forward. Designed for both agility and accuracy, this automated system not only eases the workload on humans but also enhances operational capabilities across various sectors. This article will draw you into an in-depth exploration of the Phantom Auto Forklift, covering everything from its technological underpinnings to real-world applications and the potential implications of widespread adoption.
As we delve into the heart of this innovation, it is crucial to recognize its relevance in todayâs logistics landscape. The ongoing demand for automation and efficiency has spurred interest in the development of advanced tools like the Phantom Auto Forklift. Its integration can revolutionize material handling, streamline processes, and ultimately reduce operational costs for businesses.
Software Overview
Understanding the technological fabric that makes the Phantom Auto Forklift tick is essential for grasping its full potential. At the core of this automated system is a sophisticated software suite that ensures seamless operation and adaptability.
Key Features
The Phantom Auto Forklift comes equipped with a range of features designed to optimize performance:
- Autonomous Navigation: Using advanced sensors and mapping technology, the forklift navigates complex environments effortlessly.
- Real-Time Monitoring: The software allows for real-time tracking of performance metrics, offering insights into efficiency and productivity levels.
- User-Friendly Interface: Intuitive design simplifies operation, making it accessible even for personnel who may not be deeply tech-savvy.
- Integration Capabilities: The forklift can integrate with existing warehouse management systems, enhancing overall operational synergies.
System Requirements
To fully leverage the capabilities of the Phantom Auto Forklift, certain system specifications are recommended:
- Hardware: Suitable processors, memory, and network components that can support real-time data processing.
- Software: Compatibility with warehouse management and enterprise resource planning systems is essential for optimal performance.
- Maintenance: Regular software updates and maintenance checks are required to ensure that the forklift operates at peak efficiency.
In-Depth Analysis
As the industry shifts towards smarter solutions, itâs pertinent to analyze how the Phantom Auto Forklift performs in various environments.
Performance and Usability
The effectiveness of the Phantom Auto Forklift is indeed notable. It offers rapid operation without sacrificing safetyâan important point in any material handling scenario. Moreover, feedback from users indicates a positive experience, thanks to its reliability and ease of use. Operators note that they can focus on more strategic tasks while the forklift handles repetitive, labor-intensive operations.
Best Use Cases
This innovative forklift shines brightest in several specific applications:
- Warehousing: Ideal for large-scale distribution centers needing effective inventory management.
- Manufacturing: Facilitates the transport of heavy materials between production lines, thus speeding up the overall process.
- Retail: Beneficial for stocking shelves and managing stockroom supplies efficiently.
"The implementation of the Phantom Auto Forklift not only increases productivity but reduces the strain on human workers, making it a win-win for all.â
As we continue to explore the intricacies of the Phantom Auto Forklift, one can only imagine the prospect of what automation can achieve. The push for innovation doesn't show any signs of slowing down, and with technologies like this, the future of material handling appears brighter than ever.
Prolusion to Phantom Auto Forklift
The realm of material handling is an ever-evolving landscape that has seen continuous advancements, bridging gaps between efficiency and innovation. The Phantom Auto Forklift stands at the forefront of this evolution, representing a significant leap in automation. Understanding the intricacies of this technology is vital for professionals looking to enhance productivity, streamline operations, and reduce costs in warehousing environments.
Automation in material handling is no longer a novel concept but rather a necessity, especially in large-scale operations. The introduction of autonomous solutions enables businesses to optimize their workforce while ensuring safety and reliability. This section aims to unpack the fundamentals surrounding the Phantom Auto Forklift, showcasing its benefits, underlying mechanisms, and overall significance in contemporary supply chain management.
The Concept of Automation in Material Handling
At its core, automation in material handling refers to the use of technology to perform tasks traditionally executed by humans. This shift not only improves productivity but also minimizes human error. For example, in a bustling warehouse, the reliance on manual forklifts can lead to accidents and delays, affecting the overall throughput. However, with automated solutions like the Phantom Auto Forklift, operations can run smoother.
The essence of automation extends beyond merely replacing human labor; it encompasses enhancing efficiency through precision and agility. Automated systems can run continuously, adaptively managing inventory and transferring items with unparalleled accuracy. In turn, this can significantly cut down on downtime, leading to both short-term and long-term cost savings.
Overview of the Phantom Auto Forklift
The Phantom Auto Forklift is designed to redefine how warehouses and logistics companies handle their material transportation needs. With its state-of-the-art technology, this forklift operates seamlessly within various environments. It leverages an array of sensors to navigate, ensuring that it can maneuver around obstacles without human intervention.
What sets it apart is not only its autonomous capabilities but also its ease of integration into existing systems. The Phantom Auto Forklift communicates with warehouse management systems, allowing it to align tasks with other automated solutions effectively. It opens the door for synchronizing operations, streamlining processes, and facilitating improved data analytics.
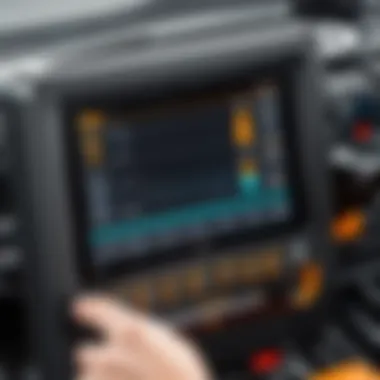
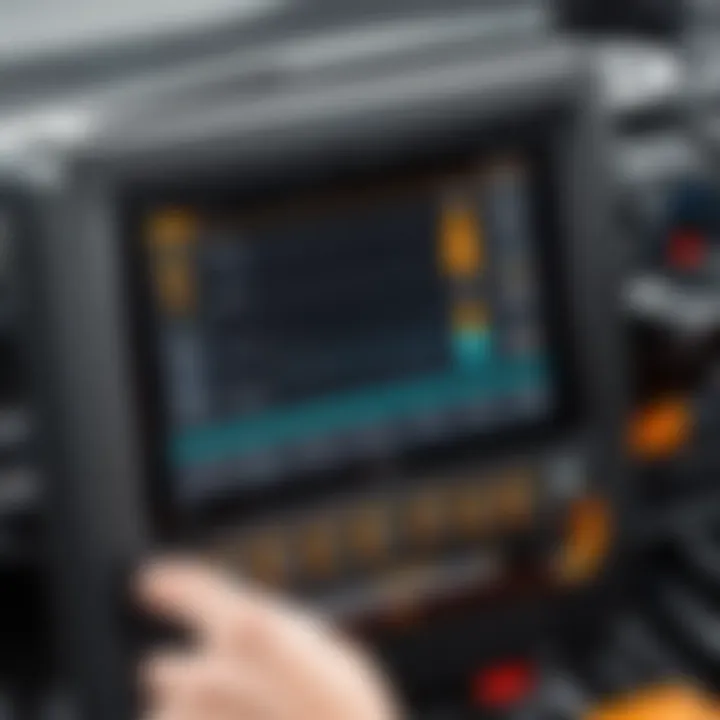
In essence, the Phantom Auto Forklift symbolizes a shift towards smarter, more efficient material handling. By examining its features and functionalities, we can uncover the profound impacts it has on industries relying heavily on logistics and distribution.
"Modern material handling demands an innovative approach. The Phantom Auto Forklift represents more than just a tool; it's a transformative technology that can reshape entire operational frameworks."
With a clearer understanding of the Phantom Auto Forklift, the following sections will meticulously explore its technical specifications, operational mechanisms, and the broader implications of its adoption in the industry.
Technical Specifications
Understanding the technical specifications of the Phantom Auto Forklift is critical for anyone looking to grasp the full scope of its capabilities in modern material handling. Delving into these specifications not only highlights the advanced engineering behind the forklift but also demonstrates how it addresses industry challenges. From motor systems to sensor technologies, each component directly affects performance, safety, and efficiency in warehouse settings. Itâs important to consider these elements not just in isolation, but as part of an integrated approach that enables seamless operation.
Motor and Power Systems
The heart of any forklift is its motor, and the Phantom Auto Forklift is no exception. Kicking off with high-efficiency electric motors, these engines are designed for longevity and reliability. The choice of power system, often involving lithium-ion batteries, plays a crucial role in enhancing the forkliftâs operational range and reducing downtime.
In a typical warehouse environment, efficiency can make or break productivity metrics. The power management system ensures that energy consumption is optimized. This can lead to significant savings on energy costs over time. Given that many forklifts used in material handling are subject to rigorous working hours, having a robust motor system means less frequent needs for maintenance, thus, saving costs in the long run.
Sensor Technologies
Imagine a forklift that can âseeâ its surroundings. Sensor technologies play an essential role in enabling the Phantom Auto Forklift to autonomously navigate through busy warehouse aisles. Equipped with cameras, LIDAR, and ultrasonic sensors, these forklifts are not left to chance. Such technologies transform the chaotic backdrop of a material handling environment into a well-ordered navigational map.
Sensors work together to detect obstacles, map out routes, and even determine load placement. The integration of these systems reduces the chance for human error, an important consideration in a setting where safety is paramount. By deploying sophisticated sensors, the Phantom Auto Forklift embodies a proactive approach to avoiding accidents, a critical concern for operators anywhere.
Navigation and Mapping Systems
When it comes to automation, navigation is where the magic happens. The Phantom Auto Forklift employs advanced navigation and mapping systems that significantly enhance operational capabilities. Utilizing technologies such as GPS, IMUs (Inertial Measurement Units), and advanced algorithms, these forklifts can create dynamic maps of their environment.
The importance of precise navigation cannot be overstated. In a busy distribution center, where multiple forklifts may be operating simultaneously, the ability to efficiently share space and maintain order leads to significant increases in throughput and decreases in operational disruptions. Moreover, the ability to learn and adapt to new layouts or changes in inventory placement further solidifies the Phantom Auto Forklift's role as a vital tool in material handling.
"The integration of advanced navigation and sensor technologies allows the Phantom Auto Forklift to operate with astonishing accuracy and efficiency, setting a new standard in the industry."
By investigating the technical specifications of the Phantom Auto Forklift, we can see the thoughtful engineering that meets the demands of modern warehousing. Whether it be through innovative motor technologies, insightful sensor integration, or advanced navigation systems, the forklift stands as a beacon of progress in automated material handling.
Operational Mechanisms
In todayâs fast-paced logistics environments, the operational mechanisms of the Phantom Auto Forklift donât just represent a leap in technology but a paradigm shift in how industries are evolving. With the growing demand for efficiency paired with cost-effectiveness, understanding the intricate workings of these autonomous lifters becomes essential. The importance here lies in how these mechanisms lead to enhanced productivity, reduced manual errors, and streamlined processes.
Autonomous Operation Capabilities
The backbone of any autonomous vehicle is its operational capabilities. The Phantom Auto Forklift shines in this area. It can traverse through designated routes without human intervention. Thanks to superior sensor fusion technology, it gathers data from its environment, processing it in real time to ensure safety and efficacy.
Moreover, the ability to adapt to different warehouse layouts offers unprecedented flexibility. Operators can easily update the routes or tasks via a centralized management interface, saving time and increasing output. Picture a bustling warehouse where forklifts efficiently handle tasks as if choreographed; thatâs the level of precision these mechanisms bring to the table.
Load Handling Features
When it comes to material handling, the Phantom Auto Forklift excels with its intelligent load handling features. With precise weight sensors, it can determine the optimal handling methods for different materials, which reduces the risk of overloading and potential accidents. The forklift can adjust its grip based on the dimensions and weight of the load, making it suitable for various items, from delicate components to hefty pallets.
Key advantages include:
- Enhanced Safety: Automatic detection of load discrepancies can prevent workplace accidents.
- Efficiency: No need for constant human oversight allows for continuous operations.
- Versatility: Capable of handling a wide range of loads without modifications.
Speed and Efficiency Metrics
Speed is of the essence in operational efficiency. The Phantom Auto Forklift operates with metrics that redefine the boundaries of whatâs possible. Equipped with robust algorithms, it manages to optimize its paths for the most efficient routes through warehouses. This not only means faster delivery times but also lowers energy consumption.
Research indicates that integrating such automated systems can improve overall productivity by up to 30% in material handling scenarios. When an operation runs smoothly, each second saved translates into cost savings and increased revenue potential.
"In a world where every second counts, the Phantom Auto Forklift stands out as a tool for efficiency that the industry canât afford to ignore."
The operational mechanisms of the Phantom Auto Forklift are not mere bells and whistlesâthey're crucial elements that create significant enhancements in material handling operations. Being aware of these functionalities gives stakeholders a comprehensive understanding of the system's potential, leading to informed decision-making in adopting automation technologies.
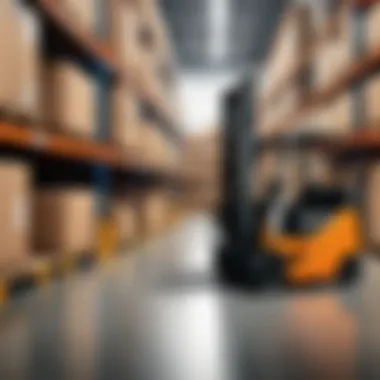
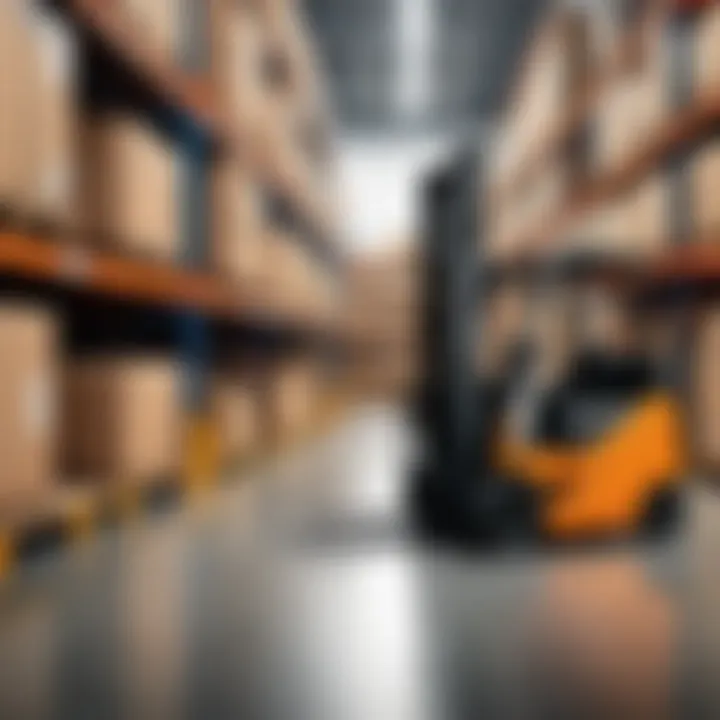
Integration with Existing Systems
In the landscape of modern warehousing and logistics, the question of how to seamlessly integrate new technologies with existing systems is paramount. The Phantom Auto Forklift, a groundbreaking innovation in material handling, must not only demonstrate its operational prowess but also prove its ability to mesh seamlessly with pre-established frameworks. This characteristic serves as a linchpin for adoption in various sectors, as it allows businesses to harness the benefits of automation without overhauling their entire operational architecture.
The integration of the Phantom Auto Forklift into existing systems offers myriad advantages:
- Enhanced Efficiency: By connecting directly with current Warehouse Management Systems, the Phantom can streamline operations, maintaining continuous data flow that optimizes inventory management and handling procedures.
- Cost Savings: Avoiding a complete system overhaul translates to reduced expenses. Companies can build upon their existing investments rather than starting from square one, thus preserving their budget structure.
- Improved Training and Adaptation: Familiarity with current systems means that staff can adapt more quickly to the introduction of the Phantom Forklift, mitigating the risks associated with extensive training of entirely new systems.
Nevertheless, integrating something as sophisticated as the Phantom Auto Forklift is not without its challenges. Companies must carefully consider the compatibility of software platforms and hardware interfaces. Technical hurdles can arise if the existing infrastructure is outdated or lacks the necessary capability to support automated solutions.
Overall, the successful integration of the Phantom Auto Forklift requires a strategic approach grounded in careful planning and assessment. By doing so, organizations can not only embrace the future of material handling but also continue to operate their legacy systems effectively and efficiently.
Compatibility with Warehouse Management Systems
At the core of successful integration lies compatibility with Warehouse Management Systems (WMS). These systems provide a structured approach to inventory control, order processing, and overall warehouse operations. The Phantom Auto Forklift leverages advanced technology to ensure that it can interface smoothly with these vital systems.
The compatibility aspect encompasses the following points:
- Data Synchronization: The Phantom Auto Forklift utilizes real-time data to inform navigation and load handling. By connecting with WMS, it synchronizes its operations to reflect stock changes immediately, ensuring accurate inventory levels at all times.
- User Interface Adaptability: The Phantom's interface is designed to be user-friendly and aligns well with existing WMS dashboards. Operators can access the data they need without the steep learning curves typically associated with introducing new software.
- Scalability and Flexibility: As businesses grow, the demand for more complex inventory management solutions increases. The Phantom Auto Forklift's ability to integrate with a range of WMS solutions makes it a flexible choice that can evolve with a companyâs needs.
In a nutshell, ensuring compatibility with WMS is essential for unlocking the full potential of the Phantom Forklift, providing businesses the agility and foresight needed to navigate a fast-paced market.
Interfacing with Other Automated Solutions
The potential for the Phantom Auto Forklift to work alongside other automated solutions is another aspect that enhances its value proposition. The modern warehouse is increasingly populated with various forms of automationâsuch as Automated Guided Vehicles (AGVs) and robotic picking systemsâthat boost throughput and efficiency.
To maximize synergy in these environments, the Phantom Forklift requires:
- Interconnectivity: The ability to share information and commands among different automated systems means that operations can become significantly more fluid. For instance, data from robotic pickers can dictate routing for the forklift, thereby preemptively optimizing workflow.
- Standardized Protocols: Using common communication protocols allows for smoother interactions and minimizes the chances of miscommunication between systems. Standard protocols can reduce the complexity of integrating disparate technologies, fostering smoother operations in warehouses.
- Real-time Monitoring: Integrating with other automated solutions creates an ecosystem where real-time data sharing is crucial. The Phantom Auto Forklift can monitor system health, operational status, and even contribute to predictive maintenance programs.
Adopting the Phantom Auto Forklift as part of a comprehensive ecosystem of automated solutions not only elevates operational efficacy but also enhances the return on investments in automation technology.
"The future of material handling lies not solely in the individual capabilities of machines but in how well they can communicate and collaborate within a larger operational framework."
This holistic approach opens doors to innovation previously deemed unattainable, placing companies at the forefront of the evolving landscape in material handling.
User Experience and Feedback
In the realm of automated material handling, the user experience and feedback are like the compass guiding the implementation of new technologies. Without understanding how the Phantom Auto Forklift interacts with its operators, we miss a critical piece of the puzzle. User feedback not only sheds light on the functionality but also influences future innovations and improvements. Itâs a two-way street; while operators benefit from efficiency and usability, developers gain invaluable insights into the machineâs practical applications in real-world settings.
Case Studies of Implementation
Examining actual case studies involving the Phantom Auto Forklift illustrates its practical value across different industries. One notable example comes from a large distribution center in the Midwest, where the forklift was integrated to streamline operations. Before its deployment, the facility struggled with bottlenecks caused by manual handling. Upon implementing the Phantom Auto Forklift, the throughput increased by nearly thirty percent, demonstrating its potential to revolutionize not just speed but also accuracy in load handling.
Another instance is found in a manufacturing plant that focuses on automotive parts. Citing safety and precision as their primary concerns, they opted for the automated forklift to reduce workplace accidents. Within just a few months, they reported a 40% decrease in incidents related to load transportation. Utilizing real-time data for monitoring operational efficiency, they adjusted their procedures based on the forkliftâs feedback, greatly improving overall safety standards.
These scenarios underline the significance of user experience as companies adapt the technology to better meet their unique challenges. Feedback from the front lines provides the raw data needed to inform tweaks and upgrades, ensuring the system aligns with users' needs.
User Satisfaction and Challenges
While the case studies paint an optimistic picture, user satisfaction levels are not universally high. Some operators have reported challenges, particularly during the initial transition period from manual to automated systems. Training requirements have been a sticking point; many workers felt overwhelmed by the learning curve associated with new technologies.
However, addressing these concerns directly is crucial. For instance, one company tackled this by implementing a comprehensive training program, tailored to accommodate individual learning speeds. Feedback indicated that as operators became comfortable, their trust in the system grew, leading to increased satisfaction.
"Initial frustration morphed into a sense of empowerment. Once I got the hang of it, I found the forklift to be remarkably intuitive," shared one operator from a restaurant supply warehouse.
On the flip side, operators have also highlighted areas for improvement. For example, some have noted that despite the technology's reliability, occasional glitches affect their workflow. Addressing these technical snags promptly is vital to sustaining user confidence and satisfaction.
Safety Considerations

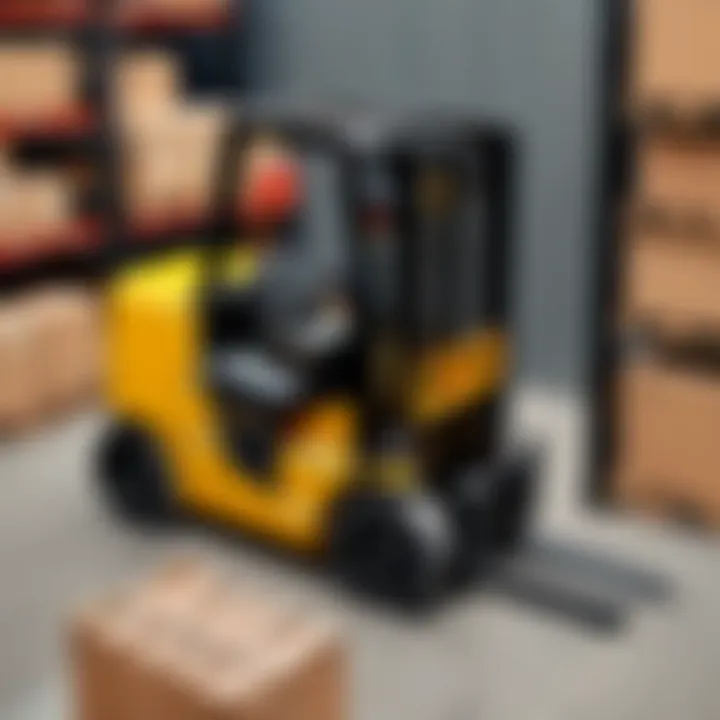
The safety aspect surrounding the use of the Phantom Auto Forklift cannot be overstated. In a working environment where heavy machinery operates, ensuring the well-being of both staff and equipment is paramount. Safety considerations not only satisfy legal requirements but also foster a culture of trust and efficiency. When a company focuses on safety, it showcases its commitment to sustainability and its workforce's welfare. The Phantom Auto Forklift, with its advanced features, is designed to mitigate risks and enhance safety protocols. Let's explore two critical areas: operational safety features and risk assessment protocols.
Operational Safety Features
The Phantom Auto Forklift is equipped with a range of operational safety features that make it stand out in the crowded field of automated machinery. These include:
- Collision Avoidance Systems: Utilizing cutting-edge sensor technology, the forklift identifies potential obstacles in its path, from employees to stacks of goods. This proactive approach minimizes the risk of accidents.
- Emergency Stop Functionality: In the event of an emergency, the Phantom Auto can be halted immediately, allowing for rapid responses to critical situations. This feature not only protects the forklift but also safeguards everything in its immediate vicinity.
- Robust Stability Mechanisms: Heavy loads can make forklifts unstable. The Phantom is designed to maintain balance, even with uneven weight distributions. Operations can proceed with less worry about tipping or accidents.
- Real-time Monitoring Software: This system continuously checks the operational status of the forklift. If something is amiss, like a malfunctioning part, alerts are sent straight to the operators.
These features work together to create a safe working environment, proving that investment in safety is not just an expense; itâs a valuable asset.
Risk Assessment Protocols
Understanding and mitigating risks are integral to the smooth operation of any automated material handling system, including the Phantom Auto Forklift. Risk assessment protocols establish a framework for evaluating the safety of operations. Here are steps typically involved in these protocols:
- Hazard Identification: Spotting potential hazards in the work environment is the first step. Knowing where issues might arise helps prepare the team.
- Risk Analysis: This involves determining the likelihood of hazards causing harm and the severity of consequences. For instance, if a sensor fails, what could that lead to in terms of accidents?
- Control Measures Development: After identifying risks, effective control measures need to be set. This can include additional training for operators or improving the forklift's existing safety features.
- Monitoring and Review: After implementing measures, itâs important to regularly review their effectiveness. Is the training working? Are the safety features functionally safeguarding users?
Risk assessments must be a living document, often revisited and revised to adapt to changing conditions and technologies. Continuous improvement in safety practices is the goal.
"Safety isn't just a priority; it's a way of doing business."
Cost Implications
Examining the financial landscape surrounding the Phantom Auto Forklift is necessary for understanding its overall impact in material handling. This section sheds light on crucial aspects like initial investment, potential long-term savings, maintenance, and operational expenses. These facets contribute a great deal to the decision-making process for businesses looking to integrate automation into their practices.
Initial Investment vs. Long-term Savings
When considering the adoption of the Phantom Auto Forklift, the initial outlay can seem steep. This investment is often seen as a hurdle, particularly for smaller operations. However, the phrase "you have to spend money to make money" rings especially true in this scenario.
Defining the initial investment isn't just about the price tag on the forklift itself. There are other costs to factor in, such as installation, training for staff, and potential upgrades for existing infrastructure. Looking at the bigger picture, itâs wise to take a closer look at the return on investment. Businesses that implement this technology can experience significant cost reductions down the line.
Research suggests that companies leveraging autonomous machinery see an average decrease in operational costs by up to 20%.
Often, these savings come from increased efficiency and reduced labor costs. The Phantom Auto Forklift can operate around the clock, minimizing down-time and optimizing workflow. This adaptability allows companies to ramp up production without linear increases in labor costs, creating an environment rich for profitability.
Maintenance and Operational Costs
Maintaining a Phantom Auto Forklift can be a cakewalk compared to traditional forklifts. These machines are designed for longevity and require less frequent repairs, thanks largely to their advanced design and streamlined components.
A bit of foresight in understanding maintenance and operational cost can lead to unexpected savings. Performing scheduled maintenance, as recommended by the manufacturer, ensures the forklift functions at peak performance. Here are some major considerations concerning maintenance:
- Predictive Maintenance: Advanced diagnostic tools can preempt any breakdowns. This approach minimizes the risk of unexpected downtime, ensuring that the forklift is always ready to hit the ground running.
- Part Replacement Costs: Predictably, the cost of replacement parts can vary. Nevertheless, sourcing them from reputable providers can save businesses from inflated prices associated with emergencies.
- Energy Consumption: The Phantom Auto Forklift is generally more energy-efficient than its counterparts. This efficiency reduces operational electricity costs over time, making it an attractive option for environmentally-conscious companies.
Thus, balancing initial expenses with anticipated savings leads to the conclusion that the Phantom Auto Forklift isnât merely a cost on the balance sheet; rather, it can be viewed as a strategic investment. Taking into consideration both upfront costs and long-term savings can indeed shift the paradigm towards adopting this kind of automation technology.
Market Trends and Future Outlook
Understanding the market trends and future outlook concerning the Phantom Auto Forklift highlights not just where the technology stands today but also where it is headed. This segment brings to light the growing relevance of automation in material handling and its far-reaching impacts across various industries. As businesses strive for increased efficiency and reduced operational costs, the demand for automated solutions, like the Phantom Auto Forklift, continues to rise.
Growth of Automation in Material Handling
The surge in automation within material handling isn't merely a trendâit's a monumental shift that's reshaping the logistics and warehouse sector. Here are key factors contributing to its growth:
- Increased Demand for Efficiency: Companies are under tremendous pressure to streamline operations and minimize downtime. The Phantom Auto Forklift exemplifies this need by enhancing productivity through autonomous operations and minimizing human error.
- Labor Shortages: The current labor landscape has left many industries grappling with a shortage of skilled workers. Automation provides a solution by filling gaps, allowing companies to maintain optimal operations without relying solely on human labor.
- Technological Advancements: Innovations in AI, machine learning, and IoT have paved the way for smarter, more efficient forklifts. The Phantom Auto Forklift, equipped with such technologies, allows for better inventory management, predictive maintenance, and real-time data analytics.
Notably, a report from en.wikipedia.org indicates that the global market for automated material handling is projected to surpass several billion dollars in just a few years. This growth hinges on the technological evolution we see today.
Emerging Technologies to Watch
The future of material handling will likely be influenced by various emerging technologies. Monitoring these will be critical for stakeholders in the industry:
- Robotics: The integration of advanced robotic systems can significantly increase the versatility and effectiveness of material handling equipment. Collaborative robots or cobots working alongside human workers will redefine how warehouses operate.
- Artificial Intelligence: AI systems will play a pivotal role in enabling predictive analytics, automated decision-making, and optimizing workflow processes. A smarter system means faster and safer operations.
- Blockchain Technology: While not directly related to forklifts, the application of blockchain in inventory management can boost transparency and traceability throughout the supply chain, adding another layer of reliability to operations.
"As automated systems become simpler and more integrated, companies can leverage these advances to enhance their competitive edge."
In summary, the trends in automation and the technologies emerging alongside this movement suggest that the future holds great promise for innovations like the Phantom Auto Forklift. Being adaptable and forward-thinking will be essential for businesses seeking to remain relevant in an increasingly automated world.